Chao Ziyi, Chao Ziwei
《青春记忆》55×60×25cm 陶瓷 2013年 作者:钞氏兄弟 第二届韩国国际陶瓷双年展“铜奖”
After China’s reform and opening-up, artists have been digging for new materials, exploring new technologies and expanding new forms in ceramics. In terms of material selection, glaze color preparation, decorative treatment, molding techniques, firing techniques and artistic concept expression, they have created art forms different from those in any previous period. Artists are becoming more proficient in the use of materials, the subject matter is more extensive than before, the molding technique is more mature, the artistic expression is more perfect, and the exploration of ceramic language is more bold, rich, and free. This article will discuss the expression and expansion of ceramic language in contemporary art creation from the specific performance of different firing techniques in contemporary ceramic sculpture combined with my own practice.
Contemporaryart, ceramic sculpture, firing technique
鈔子藝,鈔子偉
摘 要:中國自改革開放至今,藝術家們不斷在陶瓷方面挖掘新材料,探索新技術,拓展新形勢。無論是在材料選擇、釉色配置、裝飾處理、塑造手法、燒製技術和藝術理念表達上,都創造出了不同於以往任何時期的藝術形式。藝術家在材料運用上越來越豐富,題材也比以往更爲廣汎,塑造手法更爲成熟,藝術表現也更爲完善,在陶瓷語言的探索上更加大膽、豐富、自由。本文將從不同燒製手法在當代陶瓷雕塑的具體表現,結合本人的實踐對陶瓷語言在當代藝術中的表現與拓展進行梳理和探討。
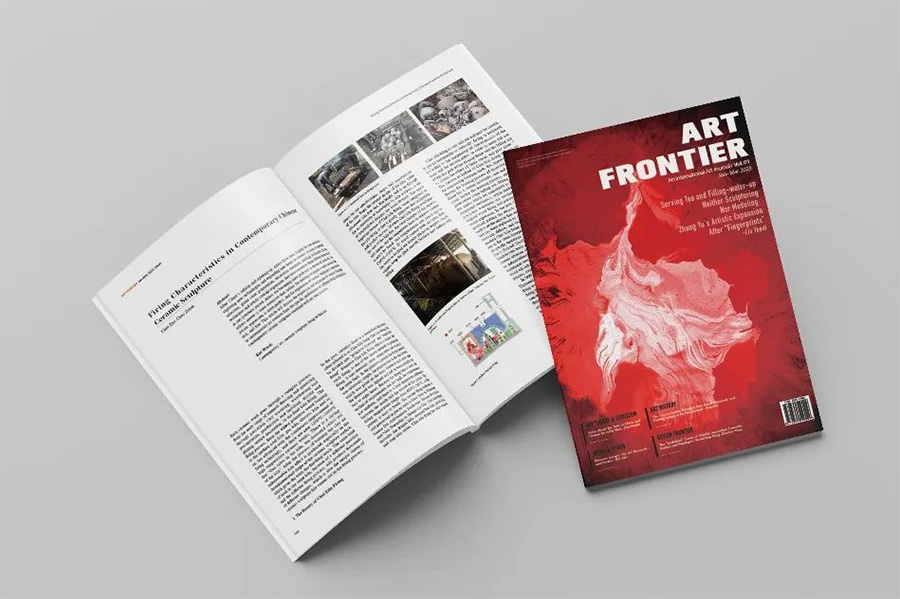

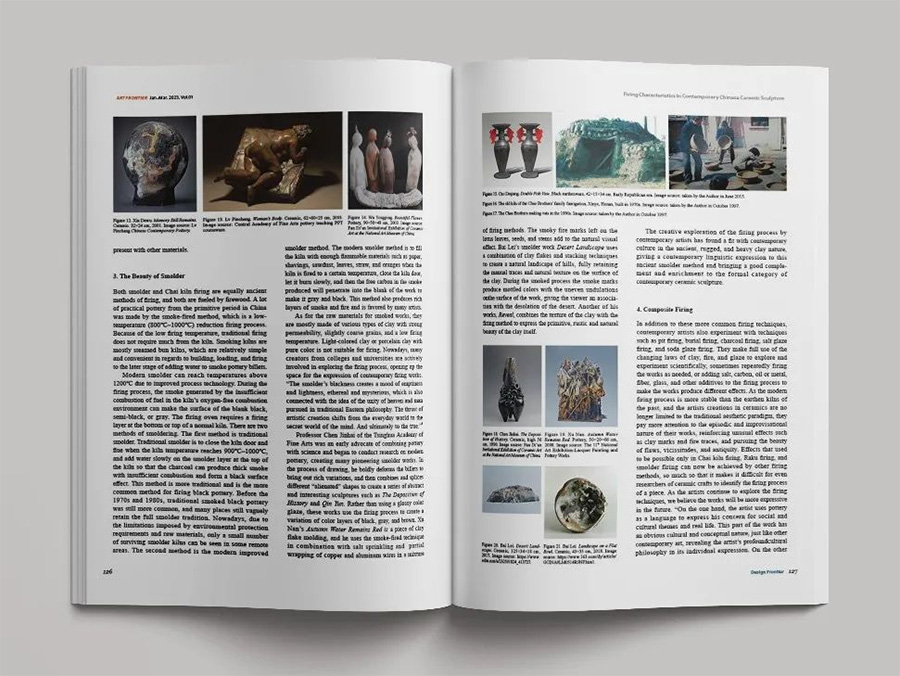
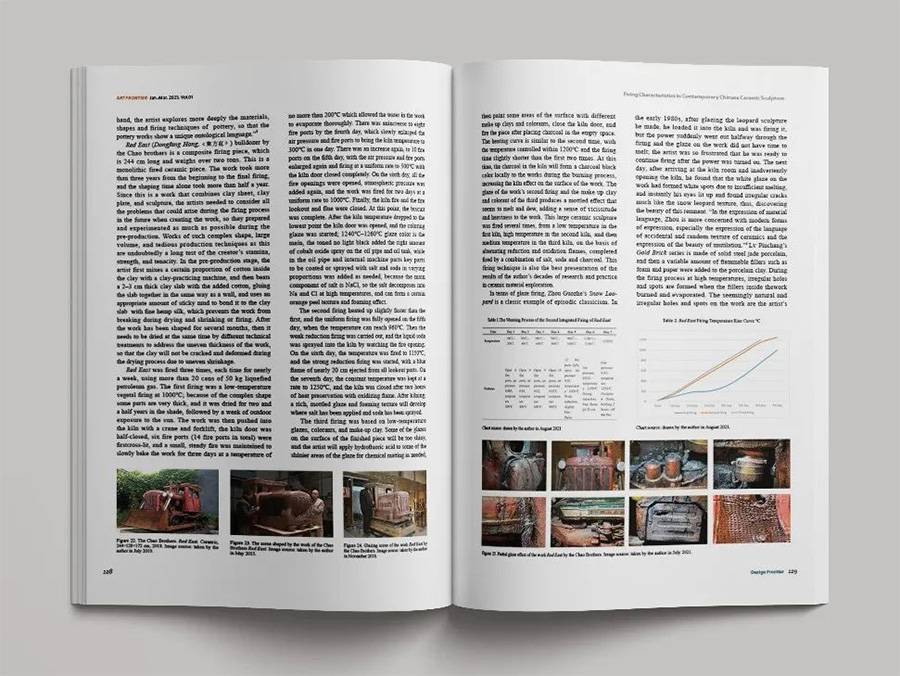

Each ceramic work goes through a complex process, from the early stage of mineral dressing and quarrying through porcelain clay washing, weathering and precipitation, production and molding, drying and glazing, texture decoration, to the final kiln firing. The firing process, from the oldest primitive wood burning to the modern coal kiln, gas kiln, electric kiln and so on, has advanced with the continuous improvement of firing technology, and there are now 1300℃–1400℃ high -temperature ceramic works. There is a saying that “One color in the kiln, ten thousand colors out of the kiln”. After the process of burning the clay an unforeseeable kiln effect is produced, especially in the three-dimensional shape of the ceramic sculpture surface, which gives the work the finishing touch. The same kind of mud in the same kiln, because of a different position and the different firing process, will produce thousands of different changes, which is also the unique charm of ceramic sculpture that comes out in the firing process.
1. The Beauty of Chai Kiln FiringIn the past, ceramics fired in a wood-fired kiln were often referred to as Chai kiln firing. Chai kiln firing can be divided into “primitive firewood” and“wood kiln firing”. Primitive Chai kiln firing, which is kilnless flat stack firing, is one of the closest methods to primitive firing. It uses firewood, straw, wheat straw and so on as the main fuels. In the primitive period, the firing method was relatively simple; the purpose was to dry the pottery, which was piled on the built firewood and straw, and the firewood was lighted and left to burn naturally for two to eight hours. Because the firing time is short, the technical requirements are not high, the combustion is not uniform, and there is a large temperature difference between the inside and the outside of the pottery. The firing temperature ranges from 600℃–1000℃, so the pottery is easy to break. The ancient firing tradition is still preserved in places such as Gasa Town in Xishuangbanna Dai Autonomous Prefecture, Yunnan Province, and Nixi Township in Shangri-La City. Chai kiln firing includes the dragon kiln, steamed bun kiln, gourd kiln, and step kiln styles. Chai kiln firing has strict requirements for the specifications, shape, and construction of the kiln. From the internal design of the kiln, billet placement, kiln door size, flue height, and so on through the accumulation of knowledge by kiln workers, a set of standardized designs has been formed. The most important feature of Chai kiln firing, when compared to flat pile firing, is that it greatly improves fuel utilization and product success. Modern Chai kiln firing combines the size of the kiln fire, the color changes of the objects and shapes, and the temperature level to achieve certain control by hand, and temperatures can reach up to 1200℃–1300℃. To avoid contact with an open fire, the wares to be fired are usually placed in saggers. Such saggers keep the glaze smooth because they reduce ash falling.
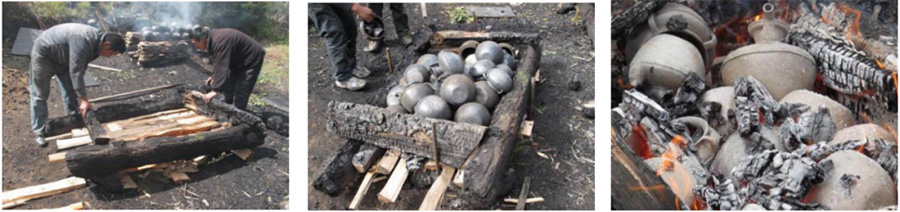
Figures 1, 2, 3. TraditionalChai kiln firing process.
圖1, 2, 3. 傳統柴燒過程 圖片來源:楊潤《麥宿藏區黑陶研究》,中國美術學院碩士論文,2012年
Figure 4. A traditional Dragon Kiln in Yantou village, Nanping City, Fujian province.
Figure 5. ModernChai kiln firing.
“Chai kiln firing is very delicate and must be carefully placed horizontally or vertically, facing or backward, according to the morphological characteristics of the work and the desired effect, in order to make full use of the fire path of the flowing flame and the falling ash to obtain the effect of flame traces and gray glaze.”1 The success or failure of Chai kiln firing depends on the relationship between earth, fire, firewood, and kiln. During the burning process of firewood, because the flame has a certain instability, soot and ash fall on the blank during the burning process, and the blank and glaze retain some falling ash, falling slag, and uneven fire marks which are considered as flaws or defects in traditional aesthetics, while modern Chai kiln firing precisely overturns the aesthetic standards of the original wood firing and pursues a unique and natural visual expression. In the past, Chai kiln firing generally involved putting the objects into a sagger to keep the surface of the objects fine and polished and perfect, and that has been replaced by new aesthetic trends such as antiquity, defects, and vicissitudes. Therefore, although modern Chai kiln firing and traditional Chai kiln firing are in the same lineage, they are very different in terms of specific operations and aesthetics. For example, Chen Jun’s Twisted Shuttle uses the “shuttle” in traditional hand-woven tools as the creative element to reveal the current situation of the survival of traditional handicrafts in industrialized society. The work was fired with the traditional wood-fired kiln process, and the grass and wood ash left uneven kiln smoke marks during the firing process, adding a sense of historical heft.In 1999 Li Zhefeng and Zhang Wenzhong planned the Thousand Year Burning, a large-scale outdoor Chai kiln firing event in Shiwan which brought Chinese Chai kiln firing from traditional to contemporary, from practical to conceptual. Among the participants of the Thousand Year Burning event were many front-line potters who were active at home and abroad. They tried to interpret the new thinking of modern peoples about ceramic cultural heritage and the contemporary language expression of pottery from different cultural and regional perspectives. Chai kiln firing, a class of firing techniques with a thousand-year heritage, has achieved a unique contemporary cultural value through the substitution of modern firing techniques. From Lv Pinchang’s Relic Object, Lu Bin’s Impression of Shiwan, Guo Xuda’s Untitled, to Liu Zheng’s Human-shaped Column, etc., most of these works start from sculptural shapes, combine with traditional firing techniques and modern concepts, find new expressions of sculptural forms, and give a new visual context to ceramic sculpture from which we can see the significance and cultural value of this event for exploring modern Chai kiln firing in Shiwan. Zhang Wenzhi mentions in “The Revelation of Thousand Year Burning” that “‘Thousand Year Burning’, as a historical event of modern pottery, triggered the modern transformation of Shiwan’s traditional ceramic art and culture, and was a time for local potters to seriously think about finding their own direction in the East and West cultural background to find their own direction and realize the transformation of tradition to modernity.”2 After the Thousand Year Burning, international ceramic cultural exchanges in Shiwan became more and more frequent, which also led more pottery creators to join the modern Chai kiln firing movement, and later slowly formed the International Pottery Village in Ancient Nanfeng Kiln. As one of the creators of Thousand Year Burning, Wei Hua established a ceramic studio in Ancient Nanfeng Kiln and started the creation of the “New Doll” series. In his later work Wall of Figurines - Tang Terracotta Wall, the doll was printed with a mold and then combined and pressed into shape, and the traditional Chai kiln firing method of Shiwan was used to fire the “doll tiles” in different shades of color, heavy and ancient, and through the overall combination the Chai kiln firing wall showed the cultural lineage and contemporary heritage of Shiwan ceramics. “Throughout this pottery creation, we can get the impression that as a result of the event, one by one, the pottery works have been permanently placed in the public space, and in this sense, the event is a success, and the pottery has really reached out to the outdoor tentacles.”3
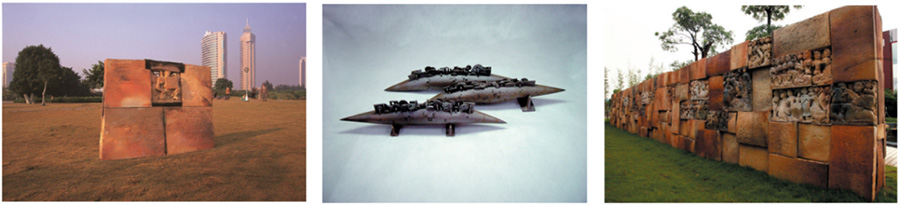
Figure 6. Chen Jun. Twisted Shuttle. Ceramic, size unknown, 2006. Image source: Courtesy of Chen Jun.
圖6.陳君《扭曲的梭》 陶 尺寸不詳 2006 年 圖片來源:陳君提供
Figure 7. Lu Bin.Impression of Shiwan. Ceramic, 200×150×30 cm, 1999. Image source : Provided by Lu Bin.
圖7.陸斌《石灣印象》拓器200×150×30cm 1999年 圖片來源:陸斌提供
Figure 8. Wei Hua. Wall of Figurines-Tang Terracotta Wall. Ceramic, 1500×25×260 cm, 2008. Image source: Courtesy of Wei Hua.
圖8.魏華《公仔牆·唐俑牆》 陶 1500×25×260 cm 2008年 圖片來源:魏華提供
Chai kiln firing, as a firing method that is both ancient and modern, combined with the artist’s sense of innovation, has established a bridge between cultural heritage and contemporary innovation, greatly enriching the expressive dimension of ceramic materials and giving new vitality to traditional Chai kiln firing.
2. The Beauty of Raku FiringRaku firing is a unique firing method that first originated in 16th century Japan as a folk sitting tea ceremony. Traditional Raku firing kilns are generally built with earth into a straight flame kiln with a short chimney, fueled mostly by pine or wood, glazed with raw lead glaze, and fired at once using medium and low temperatures. Because of the differences in glaze color, Raku firing is divided into “black Raku” and “red Raku”; black Raku firing temperatures do not exceed 1200℃, red Raku firing temperatures are in the 800℃–900℃ range to achieve the firing flame for oxidation or reduction. Raku firing is highly respected in the Japanese tea ceremony community for the special color of its firing, and it is said to be “First Raku, second Hagi, and third Saga(一樂,二萩,三唐津)”. This refers to Raku firing from Kyoto, Hagi firing from Yamaguchi Prefecture, and Karatsu firing from Saga Prefecture. Later improved by the famous American potter Paul Suttner, Raku firing was gradually applied by artists to the creation of modern pottery and is now a common firing method used by artists in the United States, Japan, Korea, and Europe, while many Chinese artists engaged in ceramic sculpture are also experimenting extensively with Raku firing.
Raku firing has certain requirements for the clay, and there are strict controls on the selection of blank clay. Clay is generally rich in minerals such as iron, manganese, and titanium. In order to express the simple, natural and unpredictable glaze color effect after firing, the operator usually uses coarse clay rich in minerals, and some operators need to add a certain amount of coarse clay or clinker. Clinker is mostly crushed ceramic waste after firing; adding clinker to the blank provides good permeability, the work is not easy to crack in the firing process with rapid heating expansion or cooling shrinkage and can effectively prevent the blank from cracking in the second firing. Rakufiring is characterized by rapid firing and a highly participatory, fun, and improvisational firing process. Raku firing is also called “happy firing” because of the unforeseen accidental effect of the glaze after the operation is completed. There are certain requirements for the size of the work, and because of the difficulty and danger in its operation, a slight mistake in operation will easily be burned by the high temperature of the kiln, so the size of the work should not be too large, generally, 20 to 30 cm in size so that it is more convenient to use the clamp to clip out; there are few works over 50 cm. Next is the choice of kiln. Theoretically, any kiln can be used for Raku firing, but since the kiln door needs to be opened or closed several times during the firing process, the blanks need to be removed from the furnace and put into the barrel in time. In this process, the rapid burning of straw or leaves in the barrel generates a lot of smoke, so modern Raku firing kilns are usually located outdoors in a well-ventilated and open area.

Figure 9. Raku firing process. Image source: Central Academy of Fine Arts pottery teaching PPT courseware.
圖9.樂燒過程 圖片來源:中央美術學院陶藝教學PPT課件
Figure 10. The creation process of Fossil by the Chao Brothers. Image source: taken by the author in September 2002.
圖10.鈔氏兄弟《化石》 陶 27×15×46 cm 2003年 圖片來源:作者拍攝於2005年8月
Figure 11. The Chao Brothers(鈔氏兄弟). Fossil. Ceramic, 27×15×46 cm, 2003. Image source: taken by the author in August 2005.
圖11.鈔氏兄弟《化石》創作過程 圖片來源:作者拍攝於2002年9月
ModernRaku firing kilns are usually built separately, in a simple and readily accessible way, and are not too large. The lower half of the furnace is stacked with high temperature resistant bricks, the upper half of the furnace is made of angle iron steel for the skeleton outside and refractory high-temperature cotton inside, and the four corners of the steel frame need to be welded with electric welding handles so that it is easy to move at any time. In the gas kiln, for example, before firing the low-temperature crackle glaze or metal oxide glaze containing lead or boron is sprayed on the surface of the work that has been burned, the work is then put into the kiln side by side, the “torch” is put into the interior of the kiln, the nozzle is lit, and the gas valve is opened fully so that the kiln fire is fully burning in the chamber and the interior heats up very quickly. During the firing process after the glaze of the piece has melted, the upper half of the kiln chamber is removed and the fiery red hot piece is clamped out of the kiln with a special fire poker. In the case of large works, the operator needs to wear protective clothing and gloves to hold the work out; if the protection is not appropriate, the operator can easily be burned when removing the work from the kiln. The work should be quickly put into a barrel full of wood chips, leaves, newspapers and other organic materials after removal, where the combustible materials in the barrel will be instantly ignited by the red-hot work and produce smoke. At this time water is quickly sprayed into the barrel, which is covered with the barrel lid. The temperature of the smoke and sparks in the barrel plummet due to the lack of oxygen in the barrel and the reduction, coupled with the process of smoke diffusion, prompts the work glaze kiln change. 15 to 20 minutes after removing the work from the barrel, you can see the formation of variable metallic lusters and color effects on the work’s surface.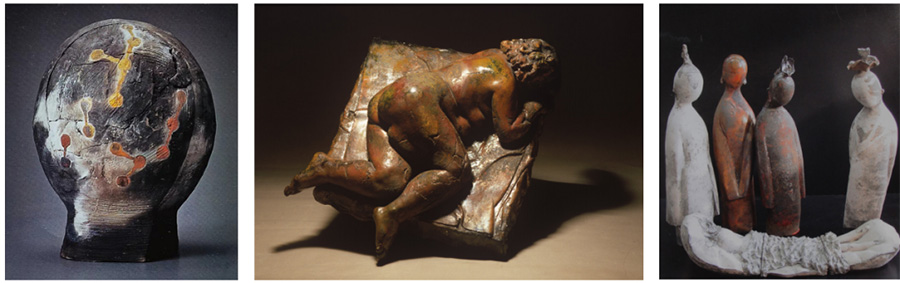
Figure 12. Xia Dewu.Memory Still Remains. Ceramic. 32×24 cm, 2001. Image source: Lv Pinchang Chinese Contemporary Pottery.
圖12.夏德武《記憶猶存》陶 32×24 cm 2001年 圖片來源:呂品昌《中國當代陶藝》
Figure 13. Lv Pinchang. Woman’s Body. Ceramic, 62×60×25 cm, 2003. Image source: Central Academy of Fine Arts pottery teaching PPT courseware.
圖13.呂品昌《女人體》陶 62×60×25 cm 2003年 圖片來源:中央美術學院陶藝教學ppt課件
Figure 14. Wu Yongping.Beautiful Flower. Pottery, 90×50×48 cm, 2003. Image source: Fan Di’an Invitational Exhibition of Ceramic Art at the National Art Museum of China.
圖14.吳永平《美麗的花》 陶 90×50×48 cm 2003年 圖片來源:範迪安《中國美術館陶瓷藝術邀請展》
It is obvious from the Raku fired works of the above artists that they are creating from a new aesthetic perspective when using Raku firing, these works also break through the old mode of thinking, and the bold exploration in glaze color and subject matter brings the viewer infinite visual imaginings which are difficult to present with other materials.
3. The Beauty of Smolder
Both smolder and Chai kiln firing are equally ancient methods of firing, and both are fueled by firewood. A lot of practical pottery from the primitive period in China was made by the smoke-fired method, which is a low-temperature (800℃–1000℃) reduction firing process. Because of the low firing temperature, traditional firing does not require much from the kiln. Smoking kilns are mostly steamed bun kilns, which are relatively simple and convenient in regards to building, loading, and firing to the later stage of adding water to smoke pottery billets. Figure 15. Cao Deqiang. Double Fish Vase. Black earthenware, 42×15×34 cm. Early Republican era. Image source: taken by the Author in June 2015.
圖15.鈔德強《雙魚花瓶》 黑陶 42×15×34 cm 民國初年 圖片來源:作者拍攝於2015年6月
Figure 16. The old kiln of the Chao Brothers’ family fumigation, Xinye, Henan, built in 1970s. Image source: taken by theAuthor in October 1997.
圖16.鈔氏兄弟家族熏燒老窯 河南新野 1970年代建 圖片來源:作者拍攝於1997年10月
Figure 17. The Chao Brothers making vats in the 1990s. Image source: taken by theAuthor in October 1997.
圖17.鈔氏兄弟1990年代做大缸場景 圖片來源:作者拍攝於1997年10月
Modern smolder can reach temperatures above 1200℃ due to improved process technology. During the firing process, the smoke generated by the insufficient combustion of fuel in the kiln’s oxygen-free combustion environment can make the surface of the blank black, semi-black, or gray. The firing oven requires a firing layer at the bottom or top of a normal kiln. There are two methods of smoldering. The first method is traditional smolder. Traditional smolder is to close the kiln door and flue when the kiln temperature reaches 900℃–1000℃, and add water slowly on the smolder layer at the top of the kiln so that the charcoal can produce thick smoke with insufficient combustion and form a black surface effect. This method is more traditional and is the more common method for firing black pottery. Before the 1970s and 1980s, traditional smoked black pottery was still more common, and many places still vaguely retain the full smolder tradition. Nowadays, due to the limitations imposed by environmental protection requirements and raw materials, only a small number of surviving smolder kilns can be seen in some remote areas. The second method is the modern improved smolder method. The modern smolder method is to fill the kiln with enough flammable materials such as paper, shavings, sawdust, leaves, straw, and oranges when the kiln is fired to a certain temperature, close the kiln door, let it burn slowly, and then the free carbon in the smoke produced will penetrate into the blank of the work to make it gray and black. This method also produces rich layers of smoke and fire and is favored by many artists.
As for the raw materials for smoked works, they are mostly made of various types of clay with strong permeability, slightly coarse grains, and a low firing temperature. Light-colored clay or porcelain clay with pure color is not suitable for firing. Nowadays, many creators from colleges and universities are actively involved in exploring the firing process, opening up the space for the expression of contemporary firing works. “The smolder’s blackness creates a mood of emptiness and lightness, ethereal and mysterious, which is also connected with the idea of the unity of heaven and man pursued in traditional Eastern philosophy. The thrust of artistic creation shifts from the everyday world to the secret world of the mind. And ultimately tothe true.”4
Professor Chen Jinhai of the Tsinghua Academy of Fine Arts was an early advocate of combining pottery with science and began to conduct research on modern pottery, creating many pioneering smolder works. In the process of drawing, he boldly deforms the billets to bring out rich variations, and then combines and splices different “alienated” shapes to create a series of abstract and interesting sculptures such as The Deposition of History and Qin Yun. Rather than using a glossy color glaze, these works use the firing process to create a variation of color layers of black, gray, and brown. Xu Nan’s Autumn Water Remains Red is a piece of clay flake molding, and he uses the smoke-fired technique in combination with salt sprinkling and partial wrapping of copper and aluminum wires in a mixture of firing methods. The smoky fire marks left on the lotus leaves, seeds, and stems add to the natural visual effect. Bai Lei’s smolder work Desert Landscape uses a combination of clay flakes and stacking techniques to create a natural landscape of hills, fully retaining the manual traces and natural texture on the surface of the clay. During the smoked process the smoke marks produce mottled colors with the uneven undulations on the surface of the work, giving the viewer an association with the desolation of the desert. Another of his works, Reveal, combines the texture of the clay with the firing method to express the primitive, rustic and natural beauty of the clay itself.
Figure 18. Chen Jinhai. The Deposition of History. Ceramic, high 56 cm, 1990. Image source: Fan Di’an Invitational Exhibition of Ceramic Art at the National Art Museum of China.
圖18.陳進海《歷史的沉積》 陶 高56 cm 1990年 圖片來源:範迪安《中國美術館陶瓷藝術邀請展》
Figure 19. Xu Nan.Autumn Water Remains Red. Pottery, 50×20×66 cm, 2008. Image source: The 11th National Art Exhibition-Lacquer Painting and Pottery Works.
圖19. 徐南《秋水殘紅》 陶 50×20×66 cm 2008年 圖片來源:《第十一屆全國美術作品展覽·漆畫陶藝作品集》
Figure 20. Bai Lei. Desert Landscape. Ceramic, 125×34×18 cm, 2017. Image source: https://www.sohu.com/a/232591824_413727.
圖20.白磊《大漠風景》陶 125×34×18 cm 2017年 圖片來源:https://www.sohu.com/a/232591824_4137
Figure 21. Bai Lei. Landscape on a Flat Bowl. Ceramic, 43×35 cm, 2018. Image source: https://www.163.com/dy/article/GCINA9LM0514R9NP.html.
圖21.白磊《平缽上的風景》薰陶 43×35 cm 2018年 圖片來源:https://www.163.com/dy/article/GCINA9LM0514R9NP.html
The creative exploration of the firing process by contemporary artists has found a fit with contemporary culture in the ancient, rugged, and heavy clay nature, giving a contemporary linguistic expression to this ancient smolder method and bringing a good complement and enrichment to the formal category of contemporary ceramic sculpture.4.Composite Firing
In addition to these more common firing techniques, contemporary artists also experiment with techniques such as pit firing, burial firing, charcoal firing, salt glaze firing, and soda glaze firing. They make full use of the changing laws of clay, fire, and glaze to explore and experiment scientifically, sometimes repeatedly firing the works as needed, or adding salt, carbon, oil or metal, fiber, glass, and other additives to the firing process to make the works produce different effects. As the modern firing process is more stable than the earthen kilns of the past, and the artists creations in ceramics are no longer limited to the traditional aesthetic paradigm, they pay more attention to the episodic and improvisational nature of their works, reinforcing unusual effects such as clay marks and fire traces, and pursuing the beauty of flaws, vicissitudes, and antiquity. Effects that used to be possible only in Chai kiln firing, Raku firing, and smolder firing can now be achieved by other firing methods, so much so that it makes it difficult for even researchers of ceramic crafts to identify the firing process of a piece. As the artists continue to explore the firing techniques, we believe the works will be more expressive in the future. “On the one hand, the artist uses pottery as a language to express his concern for social and cultural themes and real life. This part of the work has an obvious cultural and conceptual nature, just like other contemporary art, revealing the artist’s profound cultural philosophy in its individual expression. On the other hand, the artist explores more deeply the materials, shapes and firing techniques of pottery, so that the pottery works show a unique ontological language.”5
Red East (Dongfang Hong, 《東方紅》) bulldozer by the Chao brothers is a composite firing piece, which is 244 cm long and weighs over two tons. This is a monolithic fired ceramic piece. The work took more than three years from the beginning to the final firing, and the shaping time alone took more than half a year. Since this is a work that combines clay sheet, clay plate, and sculpture, the artists needed to consider all the problems that could arise during the firing process in the future when creating the work, so they prepared and experimented as much as possible during the pre-production. Works of such complex shape, large volume, and tedious production techniques as this are undoubtedly a long test of the creator’s stamina, strength, and tenacity. In the pre-production stage, the artist first mixes a certain proportion of cotton inside the clay with a clay-practicing machine, and then beats a 2–3 cm thick clay slab with the added cotton, gluing the slab together in the same way as a wall, and uses an appropriate amount of sticky mud to bond it to the clay slab with fine hemp silk, which prevents the work from breaking during drying and shrinking or firing. After the work has been shaped for several months, then it needs to be dried at the same time by different technical treatments to address the uneven thickness of the work, so that the clay will not be cracked and deformed during the drying process due to uneven shrinkage.
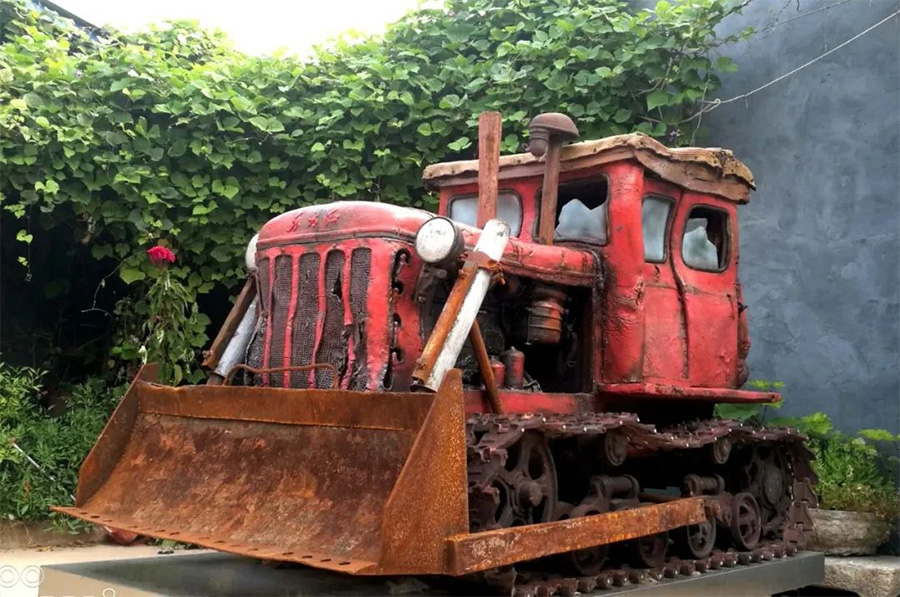
Figure 22. The Chao Brothers. Red East. Ceramic, 244×128×172cm, 2018. Image source: taken by the author in July 2019.
圖22.鈔氏兄弟《東方紅》 陶瓷 244×128×172 cm 2018年 圖片來源:作者拍攝於2019年7月
Figure23. Partial glaze effect of the work Red East by the Chao Brothers. Image source: taken by the author in July 2021.
圖23. 鈔氏兄弟《東方紅》作品的局部釉面效果 圖片來源:作者拍攝於2021年7月
Red East was fired three times, each time for nearly a week, using more than 20 cans of 50 kg liquefied petroleum gas. The first firing was a low-temperature vegetal firing at 1000℃; because of the complex shape some parts are very thick, and it was dried for two and a half years in the shade, followed by a week of outdoor exposure to the sun. The work was then pushed into the kiln with a crane and forklift, the kiln door was half-closed, six fire ports (14 fire ports in total) were first cross-lit, and a small, steady fire was maintained to slowly bake the work for three days at a temperature of no more than 200℃ which allowed the water in the work to evaporate thoroughly. There was an increase to eight fire ports by the fourth day, which slowly enlarged the air pressure and fire ports to bring the kiln temperature to 300℃ in one day. There was an increase again, to 10 fire ports on the fifth day, with the air pressure and fire ports enlarged again and firing at a uniform rate to 500℃ with the kiln door closed completely. On the sixth day, all the fire openings were opened, atmospheric pressure was added again, and the work was fired for two days at a uniform rate to 1000℃. Finally, the kiln fire and the fire lookout and flue were closed. At this point, the biscuit was complete. After the kiln temperature dropped to the lowest point the kiln door was opened, and the coloring glaze was started; 1240℃–1260℃ glaze color is the main, the toned no light black added the right amount of cobalt oxide spray on the oil pipe and oil tank, while in the oil pipe and internal machine parts key parts to be coated or sprayed with salt and soda in varying proportions was added as needed, because the main component of salt is NaCl, so the salt decomposes into Na and Cl at high temperatures, and can form a certain orange peel texture and foaming effect.
The second firing heated up slightly faster than the first, and the uniform firing was fully openedon the fifth day, when the temperature can reach 960℃. Then the weak reduction firing was carried out, and the liquid soda was sprayed into the kiln by watching the fire opening. On the sixth day, the temperature was fired to 1150℃, and the strong reduction firing was started, with a blue flame of nearly 20 cm ejected from all lookout ports. On the seventh day, the constant temperature was kept at a rate to 1250℃, and the kiln was closed after two hours of heat preservation with oxidizing flame. After kilning, a rich, mottled glaze and foaming texture will develop where salt has been applied and soda has been sprayed.
Table 1.The Warming Process of the Second Integrated Firing of Red East
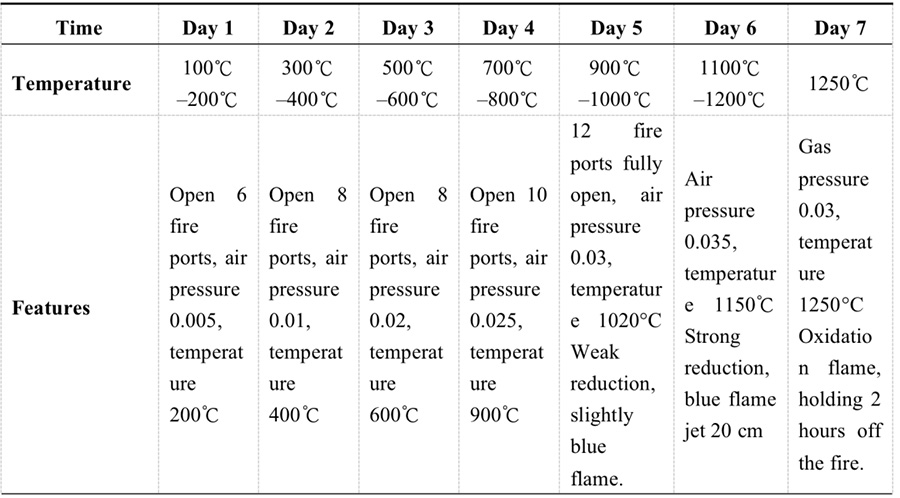
Chart source: drawn by the author in August 2021.
Table 2.Red East Firing Temperature Rise Curve ℃
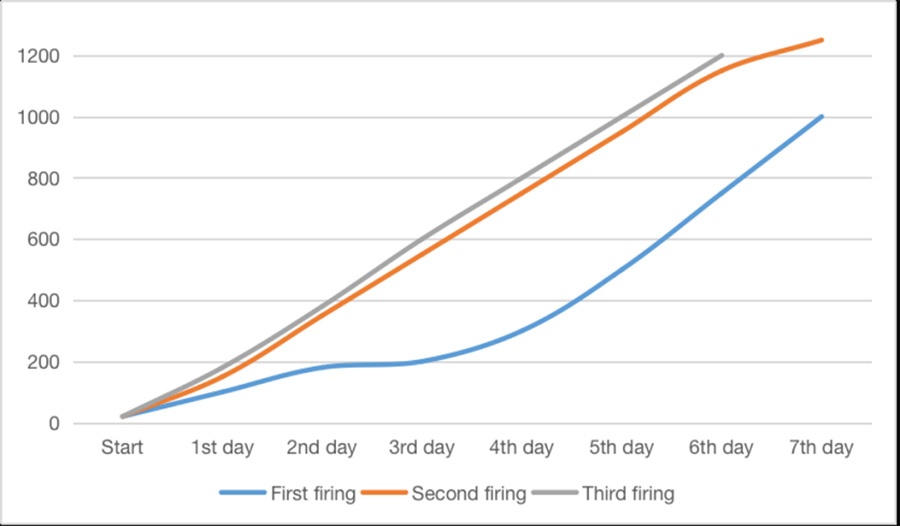
Chart source: drawn by the author in August 2021.
The third firing was based on low-temperature glazes, colorants, and make-up clay. Some of the glazes on the surface of the finished piece will be too shiny, and the artist will apply hydrofluoric acid to some of the shinier areas of the glaze for chemical matting as needed, then paint some areas of the surface with different make up clays and colorants, close the kiln door, and fire the piece after placing charcoal in the empty space. The heating curve is similar to the second time, with the temperature controlled within 1200℃ and the firing time slightly shorter than the first two times. At this time, the charcoal in the kiln will form a charcoal black color locally to the works during the burning process, increasing the kiln effect on the surface of the work. The glaze of the work’s second firing and the make up clay and colorant of the third produces a mottled effect that seems to melt and dew, adding a sense of vicissitude and heaviness to the work. This large ceramic sculpture was fired several times, from a low temperature in the first kiln, high temperature in the second kiln, and then medium temperature in the third kiln, on the basis of alternating reduction and oxidation flames, completed fired by a combination of salt, soda and charcoal. This firing technique is also the best presentation of the results of the author’s decades of research and practice in ceramic material exploration.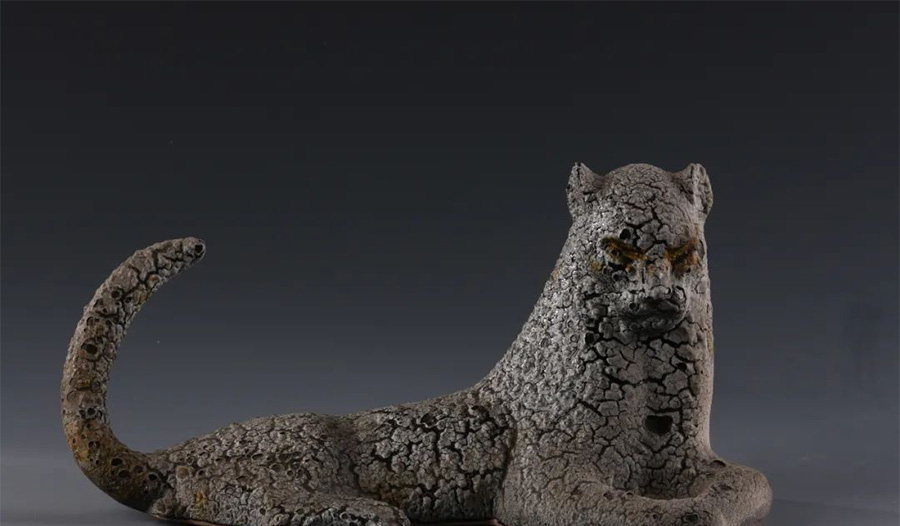
Figure 24. Zhou Guozhen.Snow Leopard. Pottery, 14.5×28 cm, 1982. Image source: Courtesy of Zhou Guojian's family.
圖24.周國禎《雪豹》 陶 14.5×28 cm 1982 年 圖片來源:周國幀家屬提供
Figure 25. Lv Pinchang. Golden Tile NO.2. Steel and Jade Porcelain, 45×45×10 cm, 2016. Image source: Lv Pinchang Haniwa Elephant: Thirty Years of Lv Pinchang’s Art.
圖25.呂品昌《金磚NO.2》 鋼玉瓷 45×45×10 cm 2016年 圖片來源:呂品昌《埴象 呂品昌藝術三十年》
In terms of glaze firing, Zhou Guozhe’s Snow Leopard is a classic example of episodic classicism. In the early 1980s, after glazing the leopard sculpture he made, he loaded it into the kiln and was firing it, but the power suddenly went out halfway through the firing and the glaze on the work did not have time to melt; the artist was so frustrated that he was ready to continue firing after the power was turned on. The next day, after arriving at the kiln room and inadvertently opening the kiln, he found that the white glaze on the work had formed white spots due to insufficient melting, and instantly his eyes lit up and found irregular cracks much like the snow leopard texture, thus, discovering the beauty of this remnant. “In the expression of material language, Zhou is more concerned with modern forms of expression, especially the expression of the language of accidental and random texture of ceramics and the expression of the beauty of mutilation.”6 Lv Pinchang’s Gold Brick series is made of solid steel jade porcelain, and then a variable amount of flammable fillers such as foam and paper were added to the porcelain clay. During the firing process at high temperatures, irregular holes and spots are formed when the fillers inside the work burned and evaporated. The seemingly natural and irregular holes and spots on the work are the artist’s further elaboration of the beauty of ceramic texture defects, and at the same time imply a reflection and perception of the long history and culture of Chinese civilization.In summary, the above explores the pioneering and development of ceramic sculpture in contemporary times from different firing processes, and more systematically sorts out the different expressive characteristics presented by contemporary Chinese ceramic sculpture. Artists have made various pioneering explorations and practices in firing, the firing method of ceramics is no longer limited to a single mode in the past, and the aesthetic language is becoming more and more inclusive, greatly enriching the modeling language and expression of contemporary ceramic sculpture. From the traditional Chai kiln firing,Raku firing, and smolder firing processes of the past to composite firing, contemporary artists have made bold attempts and breakthroughs. More than traditional firing methods, contemporary ceramic artists focus on the episodic, random, and unpredictable effects of their work in firing.
Contemporary artists pay more attention to the use of new techniques, technologies, and methods, and reinterpret and excavate through some modern techniques so that the combination of traditional firing and modern techniques presents a new meaning and form. In order to achieve a more ideal and optimal presentation, the artists even use some “destructive” means, using unconventional methods to make unexpected effects appear in their works. It is because of their bold challenges and breakthrough spirit that contemporary ceramic sculpture has taken on a richer expressive character in terms of firing.
Jingdezhen Ceramic University
THE CHAO BROTHERS (CHAO ZIYI & CHAO ZIWEI)
CHAO ZIYI (1973-), Bachelor of Science, Nanyang Institute of Technology. Member of Ceramic Committee of Chinese Culture Promotion Society. Director of Ceramic branch of China Intangible Cultural Heritage Protection Association. Member of InternationalAcademy of Ceramics. Member of Ceramic Committee of Henan Artists Association. Vice President of Chinese Overseas Artists Association and President of Sculpture Institute. Researcher of China Contemporary Sculpture Academy. Member of Chinese Artists Association. Member of China Sculpture Society.
CHAO ZIWEI (1973-), Ph.D., professor of Jingdezhen Ceramic University. Member of Ceramic Committee of Chinese Culture Promotion Society. Director of Ceramic branch of China Intangible Cultural Heritage Protection Association. Member of InternationalAcademy of Ceramics. Researcher of China Contemporary Sculpture Academy. Member of Chinese Artists Association. Member of China Sculpture Society.
Endnotes:
1. Pei Xueli. (2015). Discovering Chai kiln firing. Journal of Suzhou Art & Design Technology Institute. 4, p.94.
2. Zhang Wenzhi. (2007). The Revelation of the “Thousand-Year Firing”—A Record of the Historical Changes of Ceramic Culture in Nanfeng Guzao, Shiwan. China Ceramic Artist. 5, p.68.
3. Lv Pinchang. (1999). Modern ceramics in the outdoors: A note on the “Millennium Firing” of contemporary Chinese potters in Shiwan ’99. Sculpture. 5, p.50.
4. Yuan Hong. (2008). After Splendor, Return to Dullness. Ceramics Science & Art. 3, p.48.
5. Fan Di’an. Collection of Ceramic Art Invitational Exhibition of the National Art Museum of China. Beijing: Cultural Heritage Press. 2006, p.75.
6. Lv Pinchang. (2011). The Pioneer of Modern Chinese Ceramic Art Creation - Lv Pinchang on the Artistic Achievement of Zhou Guozhen’s Ceramic Sculpture. Art Observation. 11, p.39.
Read the "Original Text" at the end of the article to view the full paper.
Website: www.artfrontier.cn